by Ilan Garibi, edited by Sara Adams
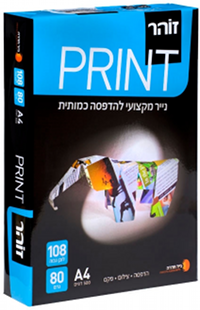
07:15. My alarm clock goes off. It's the start of an exciting day. I go over my checklist to make sure I am ready for this trip:
- one camera, fully charged;
- one framed tessellation, a gift for my host;
- some paper samples, for the laboratory tests.
I'm all set!
Hadera Paper Mill
Today I am going to visit the Paper Mill at Hadera, Israel, a town 10 km south of my home. I had folded models for the new cover design of the copy paper packages. As a gift, I received an invitation to visit the mill. Three hours later, I am by the gate. My host, Shalom, greets me and presents me with the necessary security pass.
Hadera Paper Mill has several factories and employs 800 people in total. It is a huge place. I am going to see the white paper machine. "Machine" may be an understatement since the hangar that houses it is 350 meters (382 yards) long! The Machine itself is 200 meters (218 yards) long, 4 stories high and costs around 150 million Euros (approximately 217 million USD).
The Tour Begins
Cellulose from All Over the World
The first thing I spot are the cellulose packages. Paper is made from cellulose extracted from trees. Here they work with cellulose originating from Chile, South Africa, Brazil, Canada, Portugal, and Scandinavia. The cellulose is delivered in a dry form and the main difference between the different types is the length of the fibers. In the paper industry, 3-4mm (about 1/8 inches) fibers are considered long! Short fiber cellulose comes from the harder wood, brownish or dark in color. The long fibers come from conifer. All the cellulose is from trees grown for this purpose only! Naturally grown wood is not used to make paper any more.
It's in the Mix
The first step for making paper is to dilute the cellulose in water. There are 3 containers, one for short fibers, one for long ones, and one for all recycled, raw materials. Long fiber paper is stronger and suitable for example for packing sugar. On the other hand, short fiber paper is intended for normal use, such as books and copy paper. For each type of paper, the right mixture of short and long fibers is important and it is at this stage that the mix is established.
It’s the production of printer paper we are looking at, so the mix mostly includes short fibers.
At this point, one more ingredient is added: chalk. This helps make the paper whiter and smoother, because the chalk will fill in all the spaces between the fibers.
The next step is to grind and separate the fibers into micro-fibers. At this point the mixture consists of 94% water!
The mix is then cleaned in cyclone filters. Every little stone or other impurity would cause the paper to tear and must therefore be cleared.
From Pulp to Paper
Just like when making handmade paper, it is now time to spread the mixture on a screen. When making handmade paper these screens are small enough for a person to hold and handle. Not here! The mixture is spread on a 5.2 meter (17 feet) wide and 46 meter (150 feet) long net, which is stretched over a number of drums. The mixture flows through 40 nozzles, computer controlled to ensure the pulp is distributed on the rotating screen in an even thickness. The mixture is 99.5% water at this point! This means that for every pound of paper you need around 100 pounds of water. This is the stage that consumes most water. One of the major factors in making paper ecological is re-using the water as often as possible!
At this stage some colors are added to the mixture. Every paper mill has its own combination of added colors. Here they add blue and purple. The amount is tiny, but it is enough to balance out the yellowish color of the pulp and to bring out the desired white.
And that's it! The paper is ready, but saturated with water. From now on, the machine works to remove the water. The wet paper (now 78% water) moves to the felt drums. The paper, 17 feet wide and seemingly endless, is squeezed between two layers of felt, taking out roughly half of the water. The remaining water is going to be vaporized in the oven.
Once the paper is dry, it is wetted again, but this time with starch. This will make the paper stronger. It makes sure all fibers are flattened down without any hair-like fibers remaining, which would be problematic for ink-printers; and it slows the water absorption, which is important for off-set printing.
Now, of course, the paper has to be dried again! This time a special drum is used. It's full of tiny holes and filled with high pressure air, so that there is no actual contact between the drum face and the wet paper! The paper in fact rotates on air, any contact between the sticky, starch-soaked paper and the drum surface is avoided.
The next station of the machine is all about pressing. To make sure the thickness of the paper is even, there is a sensor that measures it constantly and controls the pressure of the drums by adjusting their temperature. Simply put, if the paper is too thick, the drum is heated, therefore expanding the drum just enough to thin the paper.
The Final Result
Now it is time to monitor the final result. A line of 16 CCD cameras is continuously monitoring the paper, all 17 feet width of it. The cameras send all irregularities to a computer in the control room. The control room software looks for any patterns in the irregularities. The frequency of the problem helps to find the source for it. Since every stage in the paper making process uses drums, and every drum has a unique diameter in accordance to its function, you can deduce the villain just by examining the distance between holes or stains.
And what's the final output of the machine? It's a a roll of paper that's 17 feet wide, 31 miles long (!), and 20 tons heavy. If required, the machine can also cut it up into 14 smaller rolls.
Cutting these rolls of paper into standard-sized printer paper and packaging these is done with another machine. I have little interest in this procedure, although I can sit and stare for hours at the belt that carries the paper to be packed.
Quality Assurance Testing
I am more interested in the laboratory. Here the paper is examined and tested to measure its quality and to make sure that its characteristics fall within the required norms. The temperature and humidity in the laboratory are constantly monitored, maintaining a temperature of 22 degrees Celsius (68 degrees Fahrenheit) and 60% humidity.
Tsvika greets me, he's in charge of the quality assurance testing. But first he has to take some samples from the length of the giant paper roll. Then he starts with the water absorption test. For this he first takes a sheet of a fixed size, weighs it, puts a metal ring on it, and then adds a specific amount of water. After 45 seconds he drains the water and re-weighs the wet paper. The difference in weight reveals how much water the paper absorbed.
Next up is the tensile test machine. Tsvika puts a strip of paper, 1cm wide and 20cm long (about 0.4in by 8in), between two holding points. The machine then stretches the paper until it tears. Amazingly, the paper stretches visibly: 3.67mm (over 1/8in) along the grain! For comparison, we also test the Elephant Hide I brought along. It stretches by 17mm (2/3in) before it tears!
The final test I observe is done with a tearing machine. It measures the paper's resistance once the edge has a small tear.
And of course there are more testing machines. For example, they measure the white level of the paper, the width of it, and the angle of the curve made by the heat of a copy machine. Every aspect of the paper can be tested here, and I have full clearance to use it all. This will allow Gadi and me to scientifically enhance our Paper Review project, with accurate measurements of paper properties for Elephant Hide, Tant, Japanese Foil, Origamido, Kraft, Kami and many others.
And so the Day Ends
The trip is over. During the two hours of my visit, the machine - working at an amazing speed of 25 mph - managed to make more paper then I could fold in my lifetime! I thank my host and give him the gift, a tessellation made from Hadera paper. In return he gave me a piece of paper, 17 feet by a few yards, which he cut from the end of the roll. Sounds like a perfect paper for a 1024 grid! I guess I will be busy in this coming year...
Finally, don't forget to also read our paper review on printer paper, which is also published here!